The Science Behind Porosity: A Comprehensive Overview for Welders and Fabricators
Comprehending the elaborate systems behind porosity in welding is crucial for welders and fabricators making every effort for flawless workmanship. From the composition of the base materials to the complexities of the welding procedure itself, a wide variety of variables conspire to either intensify or alleviate the visibility of porosity.
Comprehending Porosity in Welding
FIRST SENTENCE:
Exam of porosity in welding exposes critical insights right into the integrity and high quality of the weld joint. Porosity, defined by the presence of dental caries or voids within the weld metal, is an usual concern in welding processes. These gaps, if not effectively dealt with, can jeopardize the architectural integrity and mechanical buildings of the weld, resulting in potential failures in the finished product.

To identify and quantify porosity, non-destructive screening methods such as ultrasonic testing or X-ray assessment are commonly used. These strategies enable the recognition of inner defects without compromising the integrity of the weld. By evaluating the size, shape, and distribution of porosity within a weld, welders can make informed decisions to enhance their welding processes and achieve sounder weld joints.
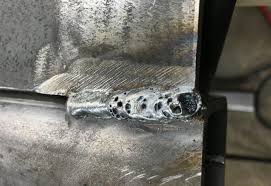
Variables Affecting Porosity Development
The incident of porosity in welding is influenced by a myriad of factors, varying from gas shielding performance to the complexities of welding parameter settings. Welding parameters, consisting of voltage, existing, travel rate, and electrode type, likewise impact porosity formation. The welding technique employed, such as gas metal arc welding (GMAW) or secured metal arc welding (SMAW), can influence porosity development due to variations in heat distribution and gas protection - What is Porosity.
Results of Porosity on Weld High Quality
Porosity development substantially compromises the structural honesty and mechanical properties of welded joints. When porosity is existing in a weld, it creates voids or tooth cavities within the product, reducing the overall stamina of the joint. These gaps act as tension focus factors, making the weld more vulnerable to fracturing and failure under tons. The existence of porosity additionally weakens the weld's resistance to corrosion, as the caught air or gases within the voids can respond with the surrounding environment, resulting in deterioration with time. Additionally, porosity can impede the weld's capacity to hold up against stress or impact, further jeopardizing the overall top quality and reliability of the welded structure. In vital applications such as aerospace, vehicle, or architectural basics building and constructions, where safety and security and longevity are extremely important, the have a peek at this site detrimental effects of porosity on weld quality can have severe consequences, stressing the importance of reducing porosity with correct welding methods and treatments.
Methods to Decrease Porosity
To enhance the top quality of bonded joints and make certain structural stability, welders and fabricators employ specific methods targeted at reducing the development of gaps and cavities within the material during the welding process. One effective method to reduce porosity is to make certain correct material prep work. This includes comprehensive cleansing of the base steel to eliminate any contaminants such as oil, grease, or moisture that could contribute to porosity development. Additionally, using the appropriate welding parameters, such as the correct voltage, present, and travel rate, is essential in protecting against porosity. Preserving a consistent arc length and angle during welding also helps in reducing the chance of porosity.

Furthermore, picking the appropriate shielding gas and maintaining appropriate gas flow rates are important in minimizing porosity. Using the appropriate welding method, such as back-stepping or using a weaving motion, can likewise aid disperse warmth uniformly and lower the possibilities of porosity formation. Finally, guaranteeing proper ventilation in the welding atmosphere to remove any type of potential sources of contamination is crucial for achieving porosity-free welds. By executing these methods, welders can successfully lessen porosity and create high-quality bonded joints.
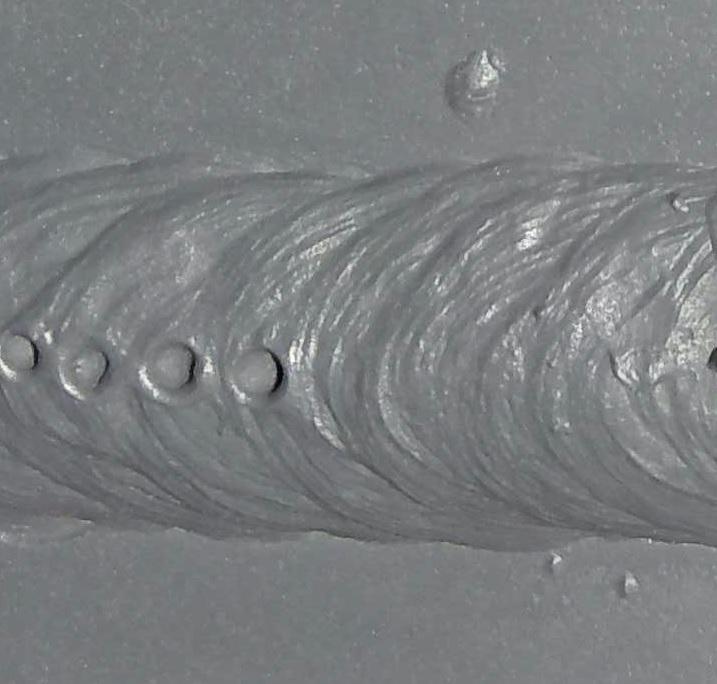
Advanced Solutions for Porosity Control
Carrying out cutting-edge innovations and innovative techniques plays click to investigate a crucial role in attaining superior control over porosity in welding processes. In addition, employing sophisticated welding strategies such as pulsed MIG welding or modified environment welding can likewise help reduce porosity concerns.
An additional advanced option entails the use of advanced welding devices. For example, making use of equipment with built-in functions like waveform control and innovative source of power can enhance weld quality and minimize porosity risks. The execution of automated welding systems with precise control over parameters can considerably reduce porosity problems.
Moreover, integrating advanced monitoring and evaluation innovations such as real-time X-ray imaging or automated ultrasonic testing can aid in discovering porosity early in the welding process, permitting immediate corrective activities. In general, integrating these sophisticated solutions can greatly boost porosity control and enhance the general quality of bonded parts.
Verdict
In conclusion, understanding the science behind porosity in welding is crucial for welders and producers to generate top notch welds - What is Porosity. Advanced solutions for porosity control can additionally enhance the welding procedure and ensure a strong and dependable weld.